Within the tight tolerances of today’s engines and transmissions, normal wear generates tiny steel particles that remain suspended in oil. These particles are so small they pass through the most advanced oil filters.
When the oil circulates back into the engine, these same particles are carried into every lubricated space. This particle laden oil will continue to lubricate, but it will also cause an exponential increase in wear while it circulates. The longer oil remains in the system, the greater the wear.
FilterMag extracts normal, wear causing, steel particles from oil with its powerful, focused, magnetic field technology without restricting oil flow.
These particles are permanently trapped on the inside wall of the filter and are thrown away when you change the filter. Slide the FilterMag off the old filter; snap it onto a new one and it goes right back to work protecting your engine.
What will your cut open filter look like?
The smaller the particles,
the greater the wear.
MacPherson proved that removal of very small particles (<10 microns) from lubricating oil has a very useful effect on the life of bearings: The finer the filtration, the longer the life.
The MacPherson Graph is based upon an accelerated test of ten rolling element bearings. The oil was contaminated with particles from gearboxes.
Removing the normal wear particles that pass through conventional oil filters will reduce wear and increase the life of your engine.
The McPherson Graph
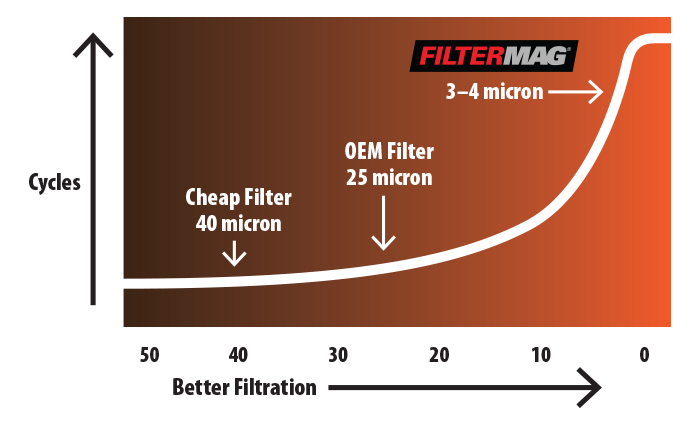
Source: Sayles, R.S., and MacPherson, P.B., “Influence of Wear Debris on Rolling Contact Fatigue,” Rolling Contact Fatigue of Bearing Steels, J.J.C. Hoo, Editor, ASTM STP 771, ASTM 1982, pp. 255–274.
Experts agree that the smallest particles produce the greatest wear.
“Particles are the primary source of wear in diesel and spark ignition engines.”
—Correlating Lube Oil Filtration Efficiencies with Engine Wear; David R. Staley, General Motors Corporation
“The significance of proliferating particles in the 10µm domain is phenomenal. Particles under 10µm cause 3.5 times more wear.”
—Review of Lubricant Contamination and Diesel Engine Wear; William M. Needelman and Puliyur V. Madhavan, Pall Corporation
”The smallest particles have the biggest effect on bearing wear. Bearing life was extended six fold by filtering to 3µm.”
—Rolling Contact Fatigue of Bearing Steels; R.S. Sayles and P.B. Macpherson
“Control of particles in the 3–10 micron range had the greatest effect in reducing engine wear.”
—Diesel Component Wear Test DDA 6V-53T Engine; AC Delco Division, General Motors Corporation
Powerful—Focused—Magnetic Field Technology
1. POWERFUL, HEAT-RESISTANT NEODYMIUM ALLOY MAGNETS are engineered to focus a magnetic field inside your filter. Specifically formulated to remain effective in the most extreme environments, our magnets are guaranteed to remove particles from oil operating at up to 300ºF while most magnets start losing magnetism at 180ºF.
2. PATENTED FLUXCON™ SHIELDING TECHNOLOGY stops magnetic flux which could damage electronic components. Not even a paper clip will stick to the outside of a FilterMag. Our FluxCon™ system also redirects a portion of that magnetic power back into the filter to increase filtration efficiency.
3. RUGGED FLEXIBLE FRAME encases and protects the elements of a FilterMag while providing enough flexibility to fit a range of filter diameters. Our proprietary design and materials are rated for temperatures from -40ºF to +300ºF.
Oil Filter History
Modern oil filters remove particles by forcing the oil through paper-based media with very small ports. The technology behind this filtering media is a compromise that has remained relatively unchanged since the 1930s. While oil is necessary to remove these damaging particles, it is equally important that it flows back into the engine fast enough to lubricate all the moving parts.
A perfect oil filter media would stop all the particles down to 1-micron (about 1/70th the thickness of a human hair). Unfortunately, a filter with ports that small would also restrict the oil from returning to the engine fast enough, resulting in catastrophic equipment failure.
Filter media developments over the years have certainly increased the life cycle for oil filtration cartridges, but fluid dynamics require the ports in the media to remain 25-micron or larger.
An SAE report by David R. Staley, General Motors Corporation, states:
“The smallest particles most popular filters captured with high efficiency are sized 25 to 40-micron, depending on the filter brand…[however] controlling the abrasive contaminants in the range of 2 to 22-micron in the lube oil is necessary for controlling engine wear.”
These tests also confirmed that removal of particles down to 2-micron in size virtually stops the abrasion wear cycle.